The FT4 Powder Rheometer® is a universal powder tester designed for measuring the properties of powder flow, and the behavior of powder.
The FT4 is a unique powder characterization, but also used as a tool for solving powder processing problems. It is different from other powder testers in numerous ways but when measuring industrial value, three features are very important:
- Application of multi-faceted powder characterization to evaluate dynamic flow, shear, and bulk properties to develop a complete understanding of how a powder behaves.
- The ability to mimic powder processing settings, by testing samples in a consolidated, reasonably aerated, stressed, or fluidized state
- Unmatched sensitivity allows the differentiation of powders that other testers categorize as identical.
The FT4 Powder Rheometer uses an exclusive technology for quantifying the resistance of the powder to flow, as the powder is in motion.
Along with the unique dynamic procedure, the FT4 also features a shear cell to measure the shear strength of the powder, and a wall friction kit to measure how the powder shears against the wall of the process equipment (as per the ASTM standard D7891). It also includes accessories for measuring bulk properties, for example, compressibility, density, and permeability.
The FT4 is truly a universal powder tester, as it offers a range of measurement capabilities. It is undoubtedly the world’s most versatile instrument for measuring and gaining insight on powder behavior.
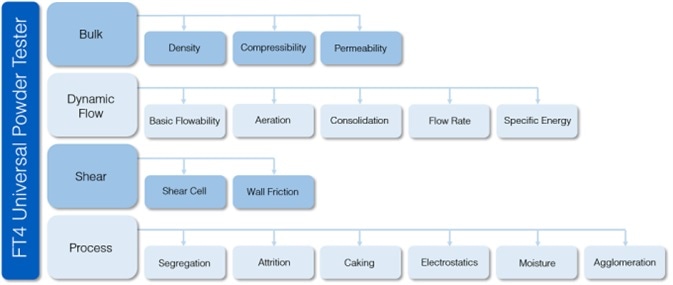
Features
- Completely automated test programs and data analysis
- Range of sample size, 10 ml to 160 ml (besides, a 1 ml Shear Cell can be chosen for limited sample size)
- Conditioning mode offers unmatched repeatability
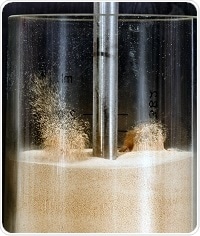
Shear Cell Testing using the FT4 Powder Rheometer
The equipment is the most professionally designed and user friendly equipment we’ve used.
Process Diversity
The nature of all processing settings is such that a range of conditions is inevitable and the powder being processed will be managed under various stress regimes. In order to fully predict the in-process performance of the powder, it is vital to measure and quantify how it reacts to each of these external variables.
External Variable |
When and where |
Effect |
Consolidation |
- Vibration / Tapping
- Direct Pressure (hopper, IBC, keg)
|
- Increase in particle pressure, contact area and number of contact points
- Reduction in air content between particles
|
Aeration |
- Gravity discharge
- Blending
- Pneumatic conveying
- Aerosolisation
|
- Reduction in particle pressure contact area and number of contact points
- Increase in air content between particles (increased porosity)
|
Flow (shear) rate |
- Within powder
- Powder against equipment wall
- Mixing
|
- Mostly non-Newtonian
- Greater resistance to flow at lower flow rates
|
Moisture |
- Storage
- Processing
- Intentionally introduced (granulation)
|
- Increase particle adhesion
- Reduced particle stiffness - more compliant but increased contact surface area
- Increase electrical conductivity
|
Electrostatic charge |
- Discharge from hopper
- Pneumatic conveying
- High shear mixing
|
- Increase bond strength between particles
- Adhesion of powder to equipment
|
Storage time |
- Raw materials / Intermediates
|
- Consolidation
- Caking
- Permanently affecting downstream performance?
|
Proven Applications
The FT4 can be used in all powder processing industries, such as pharmaceuticals, food, fine chemicals, cosmetics, metals, ceramics, toners, plastics, cements, powder coatings, and additive manufacturing (3D printing). Applications include:
- Filling
- Humidity effects
- Tablet compression
- Hopper flow
- Feeding
- Segregation
- Attrition
- Caking
- Conveying
- Milling
- Dry powder inhalers
- Electrostatic charge
- Mixing/blending
- Wall friction and adhesion
- Compact hardness and payoff
- Hopper design
- Wet granulation end point and scale up
- Flow additive selection and optimization